Brief introduction:
We are professional extrusion blow moulding machine factory and supplier in China. We can produce automatic plastic blow molding device according to your requirements. This kind of model is suitable for producing medium and small sized containers. It features fully-flash-free and highly efficient automatic long production runs. This machine is equipped with 7" monochrome LCD screen which is with human-machine interfacing control system; besides, this control system is combined with a proportional pressure hydraulic circuit. For user-friendly operations, functions of the extrusion blow moulding machine can be monitored and set on the control cabinet, such as temperature setting, hydraulic setting, flow rate setting, function setting, ALARM display, parison control, etc.
Advantages
- 1. SAVINGS: U-automatic plastic blow molding device is energy-saving, raw material-saving and labor-saving.
- 2. POWERFUL: With rapid and precise clamp force distribution, the extrusion blow moulding machine forms first-class plastic products.
- 3. PRECISE: Clamping platen parallelism is optimal for closed-loop speed and accuracy.
- 4. SERVICE-FRIENDLY: Maintenance for valves is easy and convenient.
- 5. PRODUCTIVE: Overall productivity is increased with optimized movement times.
- 6. FLEXIBLE: It applies integration of various take-out concepts.
General Features
- 1. Applying automatic computer intelligent control system with multiple language interfaces, the extrusion blow moulding machine is very convenient in operation, setting and modifying program.
- 2. Screws of the automatic plastic blow molding devices accept cold treatment, which offers superior extruding and double plasticizing effect. Besides, the screw barrel is with high wear resistance.
- 3. Patented die head is applied to conduct the deep crystal surface treatment. It is easy to refuel and change color, remove slag and clean die head. The wall thickness of tube symmetrical parts is very uniform.
- 4. When buying the U-extrusion blow moulding machines, users can choose divergent dies, spiral die, plastic extrusion dies, automatic hydraulic filter device, down blow pin, side blow pin, parison thickness controller, seal sutter, scraper and deflasher according to their preferences.
Technique Introduction
- 1. THE LINEAR CLAMPING SYSTEM
- (1) For larger automatic plastic blow molding devices from 5 liters upward, mould sizes and weight become a concern. Leshan designed linear moving clamping system applying the clamping force via a scissor toggle system. This can guarantee a total control of possible deflection by keeping the leverage ratio of the toggle arms at its best clamping performance.
- (2) In the clamping system of U-extrusion blow moulding machine, all movements are supported by linear bearings for best precision, totally absorbing any weight, and guiding the clamp in longer strokes at all times. All movements are operated almost without any friction to maintain high speed movement.
- (3) This linear clamping system is also applied to Leshan’s large 30-liter machines; however, the clamp itself is located in a diagonal box frame with direct clamping cylinders at each side. These clamping systems are available as stationary and moving carriage to suit all possible applications such as continuous and accumulator extrusion systems.
- 2. SINGLE and MULTIPLE EXTRUTION HEADS
- In this extrusion blow moulding machine, the single and multiple extrusion heads are available with side feed and center feed designs. Each head is a single head fitted to a manifold that splits the stream of melt into the appropriate number of channels. The quantity of flow in each channel is controlled by an adjusting screw. A view stripe option is available for all head sizes in single or multiple executions. All heads can be optionally equipped with an electronically controlled parison thickness programmer.
- 3. CO-EXTRUTION HEADS
- Co-Extrusion heads of Leshan automatic plastic blow molding devices are compact, reliable, and are having excellent functional capability. They allow accurate control of distribution and thickness in each layer; as this is the most critical part in the production of multi-layer containers. In U-extrusion blow moulding machine, the heads are available in versions up to six layers with a variety of output capacities.
- 4. AUTOMATIC FINISHING
- (1) For Post –Cooling, it allows a significant increase of productivity by cooling the products in a holding mask before the de-flashing process.
- (2) For Auto-Deflashing, Leshan offers 3 types of de-flashing systems; in-line hydraulic/pneumatic punching or in-line rotary cutting, and outside stand alone deflashing unit (puncher or rotary cutter). All processes can be finished within the moulding area.
- 5. EXTRUDER
- (1) Extruder drives of Leshan U-extrusion blow moulding machines are available with a hydraulic motor or inverter-controlled electric motor. The speed of the screw can be adjusted smoothly from the front operating panel. Each heating zone of the extruder is controlled individually and is usually supplied with a cooling fan to steadily control the heating parameters.
- (2) U-automatic plastic blow molding devices’ screws are available in various executions with an effective 24D length. The optional features are available such as mixing tip and shearing zone, individually or in combination to ensure a perfect blending of material and coloring agents. Screws are produced by special material and treatment for durability and longevity.
- (3) The grooved barrel force the material to be homogenized with only little compression to ensure no friction builds up. Thus the complete extruder unit can function with the minimum wear & tear.
- 6. HYDRAULIC SYSTEM
- The hydraulic components of the U-extrusion blow moulding machines are supplied mainly by the world famous brands: Bosch Rexroth, Yuken, etc. LESHAN has joined hands with these suppliers in developing a new cost-efficient hydraulic system. Also, commitments from these suppliers serve well to the benefit of our users to get the fastest possible response for spare parts and service around the world.
Maintenance
We provide one year equipment warranty, free installation for domestic market, for charging debugging in oversea market and all-life services. Equipment parts of U-extrusion blow moulding machines are free replacement for one year except for the rapid wear parts.
Packaging and transportation:
Equipment: Packed with Moisture-proof Film
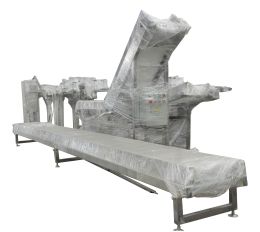
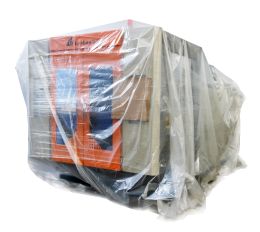
Light Spare part: Packed with Carton
Heavy Spare part: Packed with Wooden Case
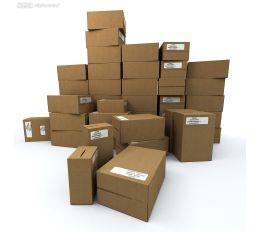
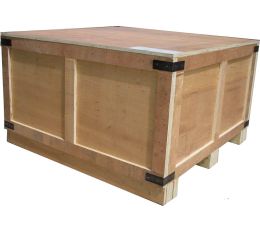